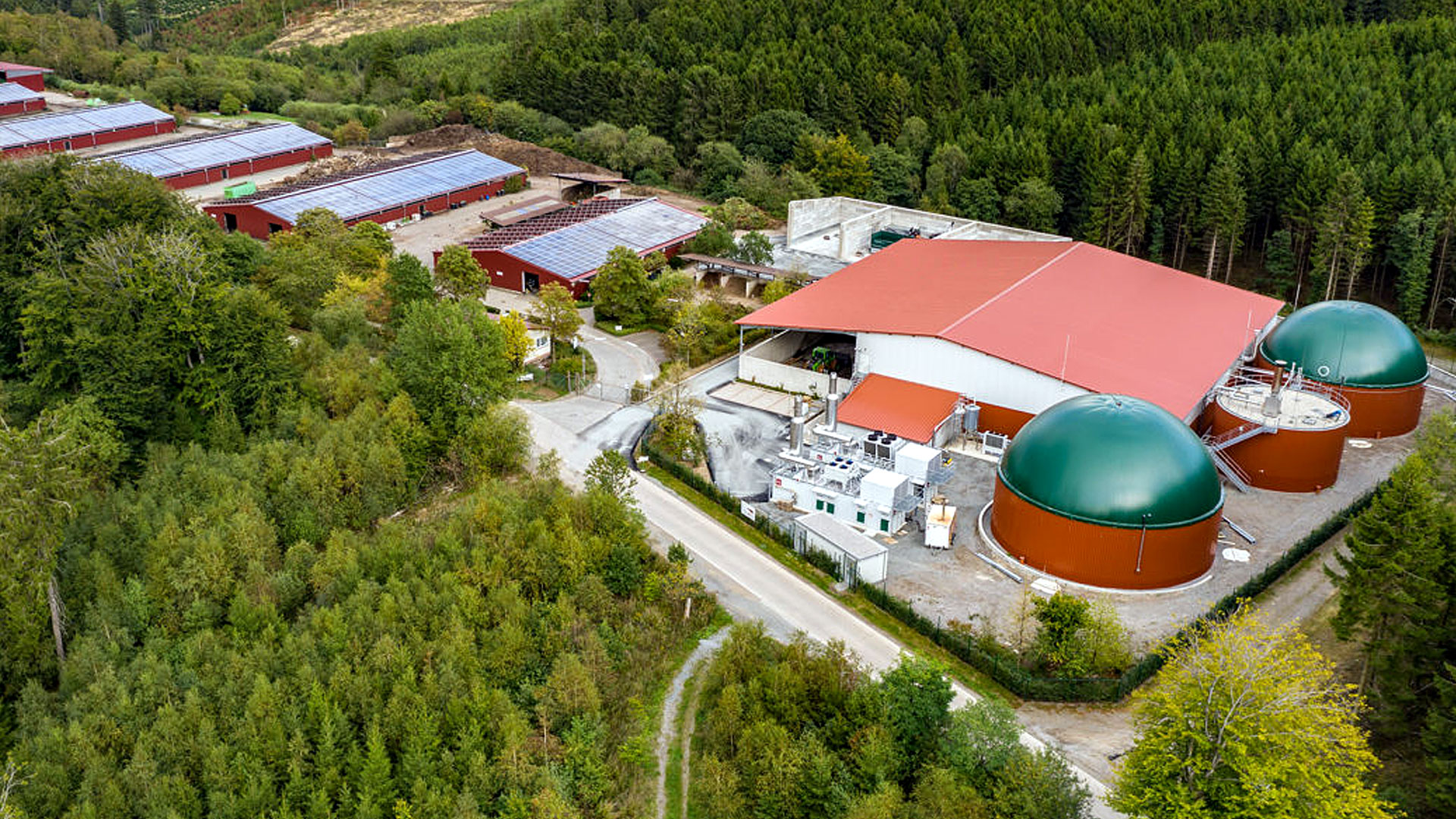
Location: | Sundern, Germany |
---|---|
Biomass: | Biowaste and green waste |
Quantity: | 22.000 t/a |
Biogas: | 2.200.000 Nm3/a |
Performance: | 580 kW el. Ø |
BIOGAS PLANT & COMPOSTING SITE
Sundern, Germany
The Biogas Plant in Germany: Harnessing Immense Potential. With the implementation of mandatory separate collection of biowastes for private households, there has been a notable increase in the amount of biowaste collected annually, reaching 4.35 million tons in 2017. Despite this, the current infrastructure reveals a disparity: for every 1,000 composting plants, there are only approximately 100 dedicated fermentation plants. This indicates that a significant portion of organic waste is solely composted, overlooking the potential energy generation through biogas plants. For waste management companies aiming to ensure their sustainability, investing in biogas plants represents a forward-thinking strategy.
Embracing this vision, Reimund and Friedrich Klute established a facility in Sundern, located at Hellefelder Höhe. Here, they process approximately 22,000 tons per annum of biowaste from the local area using a solid matter fermentation plant. Post-fermentation, the material undergoes further processing in compliance with the Closed Substance Cycle Waste Management Act, exemplifying a holistic approach to waste management and energy utilization.
Biogas Plant Powers 1,250 Households with Flexible Electricity
Our state-of-the-art biogas facility is a testament to sustainable energy production. The biogas generated at this plant is efficiently converted into electricity through two combined heat and power (CHP) units. These units are not only capable of producing electricity but also generate a significant amount of heat. This dual output enables us to supply electrical energy to approximately 1,250 households. Additionally, the heat produced is crucial for maintaining the fermentation plant’s process temperature at 52 °C (thermophilic) and for heating nearby structures.
Fermentation, unlike composting, is a process where microbial decomposition of organic materials occurs in an oxygen-free (anaerobic) environment. In this controlled, warm, and humid setting, a combustible mixture of biogas, comprising about 55% methane (CH4) and 45% carbon dioxide (CO₂), is produced. Interestingly, the biogas potential of a full 120-liter organic waste bin is comparable to the energy content of about 3-4 liters of heating oil, highlighting the efficiency of our biogas production process.
Digestion Process
Located at Hellefelder Höhe in Sundern, Germany, our biogas plant represents a pinnacle of renewable energy technology. Here, the biowaste undergoes a meticulous preparation process, initially being cleared of contaminants. It is then methodically layered in the next available digester box to a height of approximately 2.5 meters using a wheel loader. To maintain efficiency, we conduct two digester changes per week, involving both emptying and refilling. Each digester box is sealed airtight with an inflatable circumferential seal on the gate, ensuring optimal conditions for fermentation.
Our plant utilizes a unique solid matter fermentation method that forgoes the need for intricate pumping and stirring technology. During the 21-day retention period, the organic material remains static, promoting a more natural decomposition process.
The key to initiating and sustaining the microbial breakdown is the circulation of a process liquid, known as percolate. This percolate, rich in heat, microorganisms, and nutrients, is essential for the biogas production. It’s sprayed over the biomass, recollected, and redirected back to the percolate tank. After about two weeks, we observe a marked decrease in gas production, indicating the nearing completion of the decomposition process. Post 21 days, the fermented residue is extracted, dewatered, and segregated. The solid portion is sent to an adjacent composting facility for further processing, while the liquid is re-fermented in a secondary fermenter for an additional 14 days to maximize gas extraction. Finally, the processed liquid is stored for subsequent use as a high-quality agricultural liquid fertilizer.